摘要:
[1]。
目前薄膜电容在很多行业以其高耐压、高安全性能指标占领了大部分市场, 但在一些特殊应用场合, 大容量电解电容仍具有相当的应用前景, 对其正确的应用手段仍不容忽视。
本文从DC-Link电容的串并联和结构散热方式两方面, 结合纹波电流对电容温升的影响, 从实际应用的角度, 提出一种电解电容的串并联及散热结构方式, 有效地解决了电解电容的发热问题, 同时也提高了其安装牢固性及拆装便利性。
式中:f—电容两端纹波电压频率;tanδ—介质损耗角正切值;U—电容两端纹波电压值。
同时,
式中:Resr—等效串联阻抗。
结合式 (1) 和式 (2) 得到
式中:I
c—电容上的纹波电流。
由式 (3) 可以看到, DC-Link电容损耗跟流过其两端的纹波电流及电容自身参数有关。
需要指出的是电解电容的总温升实际是由两部分组成:一部分是由纹波电流与R
esr产生的损耗引起, 另一部分则是由漏电流损耗引起。但是后一部分损耗相对较小, 通常忽略不计。
根据文献[2]和文献[3], DC-Link电容纹波电流有效值为
式中:
λ—Δu/U
max;
Δu—直流母线电压波动;
U—电容两端纹波电压值;
f
s—整流输出频率;
t
c、t
f—直流母线电容器充、放电时间;
I
o.rms—逆变输出电流额定值;
M—调制比;
cosφ—功率因数。
结合式 (3) 、式 (4) 可知, 电容损耗与纹波电流、R
esr的变化成正比, 与容值、直流电压波动、功率因数、调制比、电容内部参数等均相关
[6]。
表1 电解电容参数表
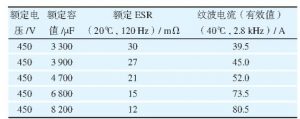
综合考虑, 以下面2种选型方式为主。
方案1:
额定容值为8 200μF、直径90 mm的电容, 采用3串2并方式, 总容值为
8.200×2/3≈5.4 m F
总纹波电流承受能力 (有效值)
80.5×2=161 A
根据式 (3) 、式 (4) , 纹波电流为
I
c≈165 A
则每串电容的纹波电流值为
I
c1≈82.5 A
那么, 单位面积的损耗为
P≈267.8 W/m
2方案2:
额定容值为3 900μF、直径64 mm的电容, 采用3串4并方式, 总容值为
3.900×4/3=5.2 m F
总纹波电流承受能力 (有效值)
45×4=180 A
则每串电容的纹波电流值为
I
c1≈41.25 A
那么, 单位面积的损耗为
P≈148.7 W/m
2由以上数据可知2种方案的总容值都满足系统需求, 但方案2的总纹波电流承受能力比方案1大12%, 单位面积损耗较方案1小80.1%。
在同一个体积中, 2种方案的结构布置如图3所示。
[7]。
电解电容正负极端子分别从正、负极箔中引出, 由于电解质中通常采用电解液作为电解质, 而电解液由铝外壳承装, 因此电解电容的铝外壳与负极端子相连通。铝外壳底部留出的固定螺柱内部凸起与负极金属箔紧密连通, 一方面加强金属箔和电解纸的安装固定;另一方面, 将金属箔上的热量以导热的形式传递到铝外壳上进行散热, 避免内部芯子热量集中而导致温升过大。
由于铝外壳与电极负端子相通, 为安全起见, 铝外壳外面通常采用绝缘套管包裹, 且铝外壳内侧壁与金属箔之间存在5 mm左右的间隙 (保证电解液的流通) 。电解电容主要的发热源为中间的芯子部位, 主要的散热形式有: (1) 通过铝外壳底部内侧凸起与芯子的紧密接触形成导热, 通过外壳进行散热。由于铝外壳外面包裹了绝缘套管, 很大程度上增加了散热热阻, 散热效果不佳。 (2) 通过铝外壳底部外侧固定螺栓与空气直接接触散热。由于该处螺栓散热面积有限, 且通常采用绝缘板安装固定, 与空气接触面积大大减小, 散热效果受到了极大限制。 (3) 由于电解电容正负极端子是采用铝箔引线连接到正负极金属箔上, 能够很好地将热量引出到正负极端子上, 而正负极端子与铜材料的复合母排紧密接触, 能够很好地将热量引出到铜母排上进行散热, 有一定的散热效果。
下面针对上述的2种串并联方案进行具体分析。
方案1:
布局如图4, 采用常规的散热方法, 即强迫风冷, 对电容圆柱外壳进行吹风散热。电解电容安装在四周封闭固定板风道中, 侧面安装2只风机进行抽风散热, 如图5所示, 风机额定流量1.92 m
3/min, 进口风速约4 m/s。