随着近年来电子技术的迅猛发展, 大功率器件和集成电路的使用越来越广泛。功率器件 (如IGBT功率模块) 有着广阔的发展和应用前景。根据著名的“摩尔定律”推算:芯片上的晶体管每18个月翻一番[1]。对于IGBT这种大功率器件, 在其正常工作时, 大功率损耗会产生大量的热从而造成自升温, 如果电源结构设计不当, 那么开关器件所产生的热量将不能及时排出, 开关器件的失效率将随着温度升高而大幅增大[2]。研究资料表明:半导体元件的温度升高10℃, 可靠性降低50%[3]。温度的上升直接影响IGBT的热应力, 严重时还会因温度过高而烧毁开关器件, 直接影响到电源的寿命和可靠性[4]。随着开关电源不断朝着大功率、高频和高功率密度的方向发展, 散热设计已成为影响电源可靠性的一个关键因素[4]。因此, 有必要对IGBT这种大功率器件的散热特性进行测量和分析, 并对其散热器的结构和运行参数等的优化进行研究。
当前流行的热设计软件种类比较多, 主要有ANSYS、FLOTHERM和Icepak。相比之下, FLOTHE-RM和Icepak在这方面显示了专业热分析软件的优越性。两者都具有专业的流体动力学CFD (conputational fluid dynamics) 的求解器, 能够分析各种流体状态, 同时, 它们提供了电子设备热分析中常见的所有组件, 使得电子设备热分析的建模非常简单。Icepak软件除了具有以上优点之外, 由于它所用的求解器为FLUNT求解器, 还具有计算精度高的优点。
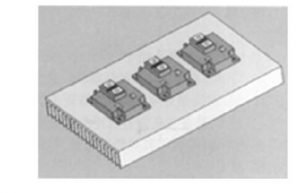
图1 IGBT散热器安装示意Fig.1 Configuration of IGBT heat-sink
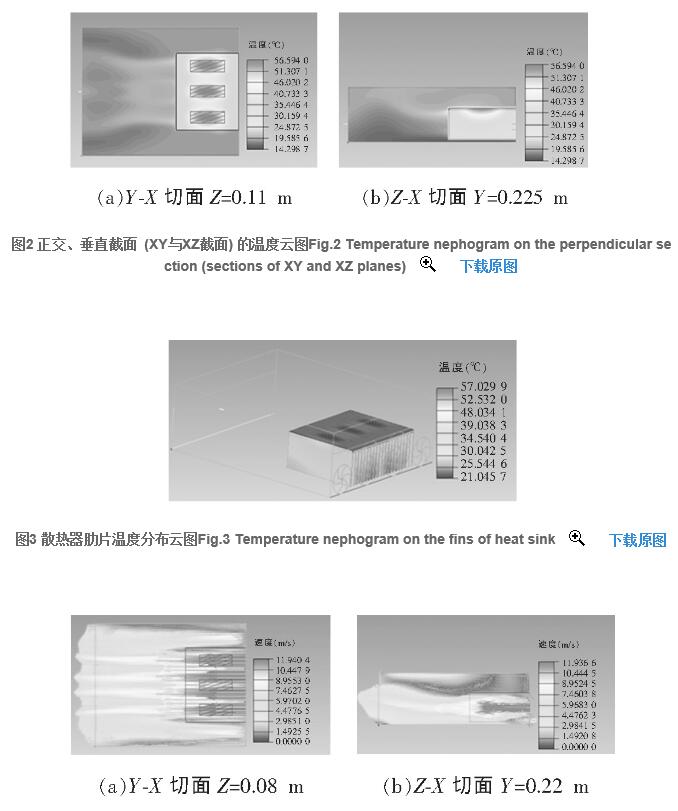
图4 正交垂直截面 (XY与XZ截面) 的速度矢量图Fig.4 Vector diagram of velocity on the perpendicular section (sections of XY and XZ planes)
由图2 (a) 中可以看出, 发热元件IGBT中心最高温度为57℃, 说明这种散热方式达到了控温目标。图2 (b) 为Z-X切面Y=0.225温度云图, 从图中可以看出, 温度流向是逐渐向远离发热元件方向发展的, 热量沿散热器扩散到空气中。空气由风机进入机箱内, 带走散热器的热量后, 再经出口流出。
该机箱采取翅片式散热器设计, 风机强化对流换热措施。散热器中流阻较大, 使得流线向散热器上下两个方向偏折, 减少了通过散热器的流量。图4为Y-X切面Z=0.08速度矢量和Z-X切面Y=0.22速度矢量图。可以看出, 空气的流向是由风机入口进入, 从出口流出。在散热器翅片间空气流速达到最大, 有利于散热器上的热量扩散。
利用K型热电偶测温仪, 在机柜组装时, 将热电偶测量探针预留在IGBT模块处, 利用导热硅脂固定。整机运行4 h温度稳定后, 用热电偶测温仪读取3个IGBT温度。
对公司主要产品最高设计温度范围进行了汇总整理, 一般室内使用温度范围0~45℃。除去军用产品, 主要产品一般使用最高环境温度为45℃, 因此, 本文研究的散热器最高使用环境温度按45℃设计。当环境温度为最不利45℃时, 热源中心最高温度达到87.2℃, 散热器平均温度为64℃。按照目前的方案, 散热已经处于临界状态, 如果使用环境更为苛刻, 则无法满足需求。另外, 从产品可靠性方面考虑也需要更优化的散热结构。
在原模型的基础上对散热器几何尺寸及风机进行优化, 通过对各种情况下的散热器热阻的比较, 得出最优几何尺寸及匹配风机。散热器由肋片和基座构成, 主要的几何参数包括肋片长、肋片厚, 肋片数、基座厚、基座宽等。确定散热器优化设计软件采用的Icepak软件, 它采用计算流体动力学求解器, 有限体积法, 非结构化网格可以逼近复杂的几何形状, 同时能实现散热器肋片高度、厚度等几何参数的优化。同时还需要考虑以下几点:安装散热器允许的空间、气流流量和散热器的成本等。
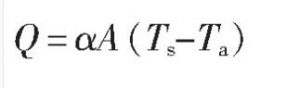
散热器热阻表达式为
在散热器优化设计软件中, 其他几何参数和环境条件均保持不变, 分析肋片高度不同时, 散热器热阻和热源中心最高温度的变化, 分析结果如图5所示。
(2) 风机风量越大, 散热器热阻越小, 温度持续降低。风量增大到0.38 m3/s后, 热源中心温度和散热器平均温度呈降低趋势, 但降低趋势逐渐减缓。